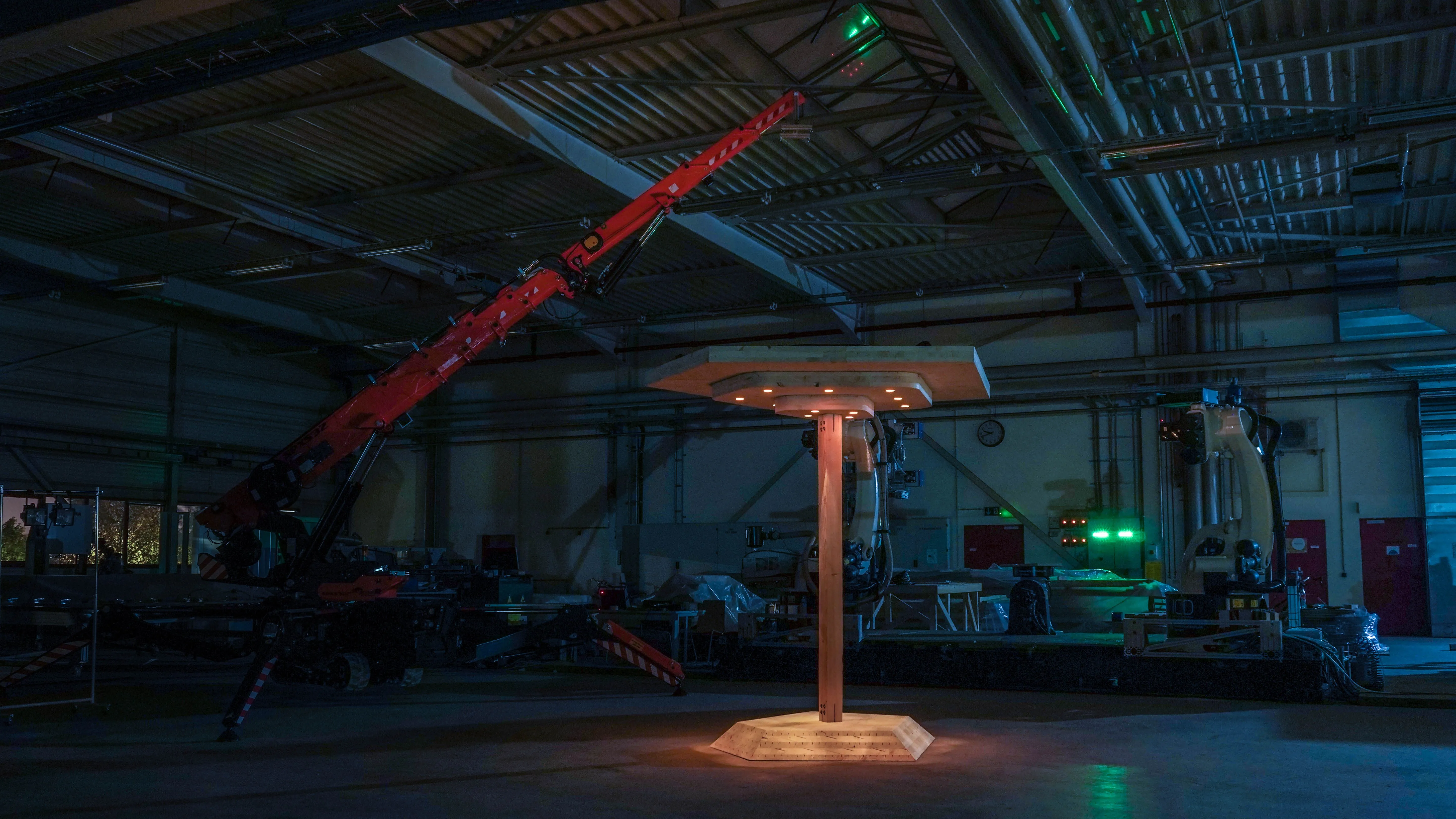
Building Across Scales
Date | 2021-10-01 |
---|---|
Authors | Daniel Locatelli, Nils Opgenorth |
Place | ITECH - University of Stuttgart |
Link | Building Across Scales at ITECH Thesis Projects |
Building Across Scales - A Robotic Timber Fabrication System for On-Site Press Gluing
The research proposes a heterogeneous multi-scalar robotic construction system to further automate on-site timber construction. Specifically, it presents the next step in the automation of on-site gluing through the introduction of a custom robotic clamping device for the on-site pressuring of timber elements. Therefore at the core of the research, lies the development of the clamping robot as part of a larger robotic construction team including an industrial robot and crane in co-design with the material and building system.
Engineered timber has opened up new possibilities in the way modern timber structures are built and designed. By simply stacking timber planks on top of each other and cross-laminating them together, it is possible to achieve strong bonding between the individual layers. However, due to transportation restrictions these timber elements are limited in size, which therefore produces modular building pieces. As this presents a weak joint between the members on-site, it consequently limits the system to a linear span and results in a grid-based architecture. This research introduces an on-site fabrication system as a strategy to go beyond these limitations. Through the integration of construction logics into the material, it presents an approach to achieve high precision during assembly and to automate the operation of a crane. Enabled by the robotic clamp it aims to continue the cross-lamination fabrication logic of engineered timber on-site to create a quasi-monolithic slab. This allows for a point supported timber slab of unlimited dimensions, which opens up for more design flexibility in the floor plan and extends the architectural design space.
PDF of the full master thesis.
Thesis Advisers: Samuel Leder, Hans-Jakob Wagner
Thesis Supervisor: Prof. Achim Menges
Second Supervisor: Prof. Jan Knippers
with support of: Bernhard Rolle (ISYS, University of Stuttgart)
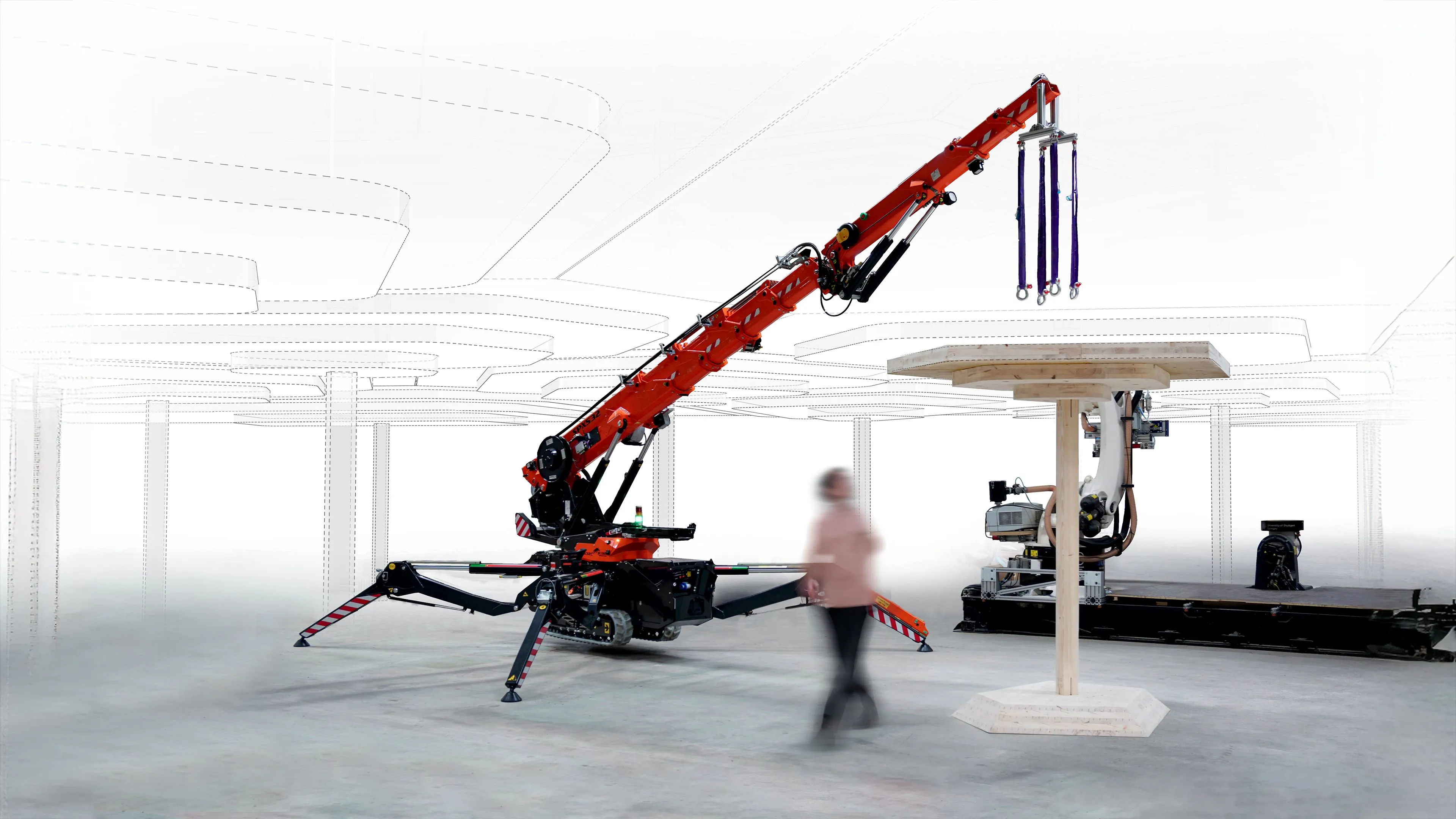
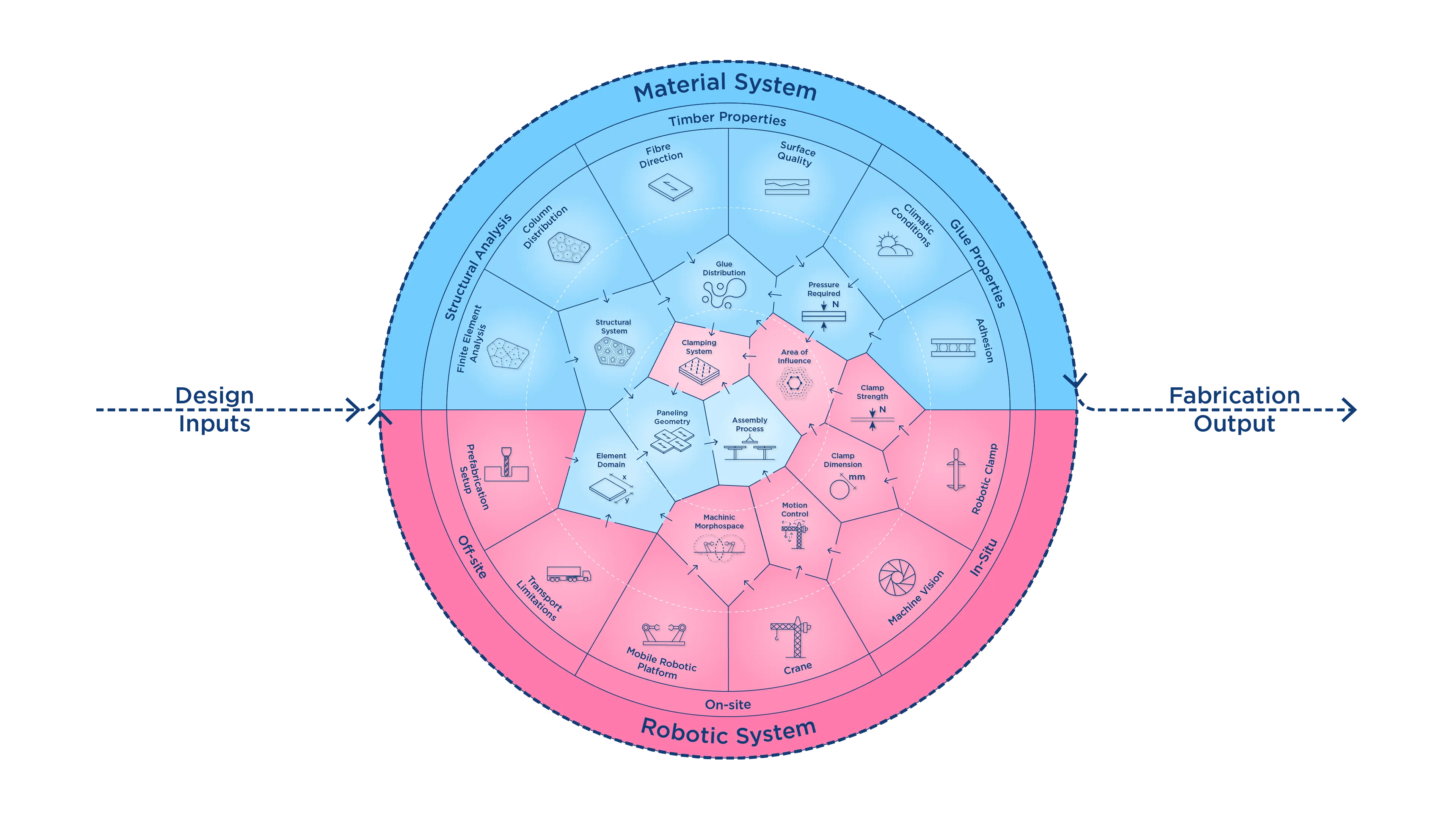
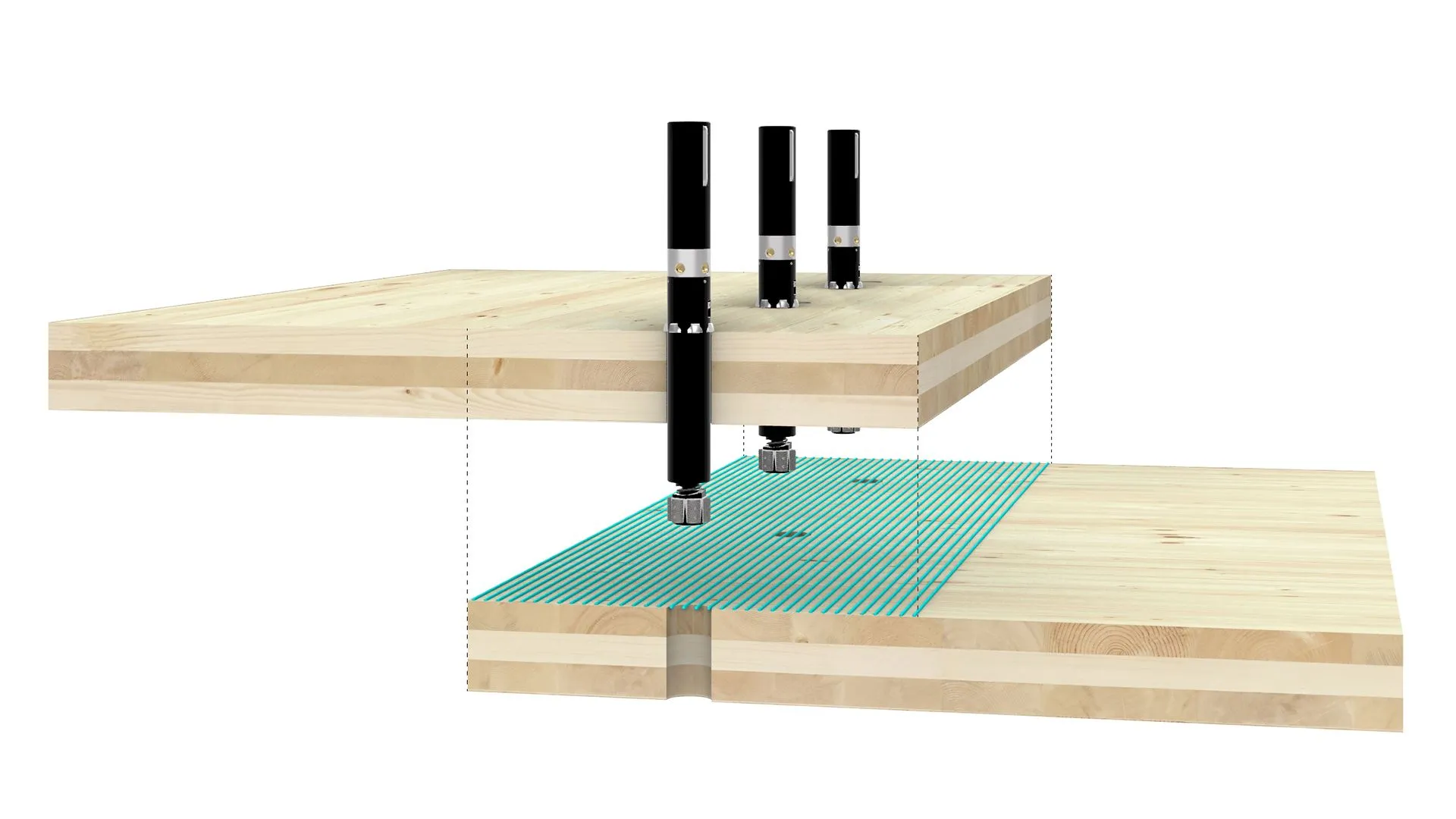
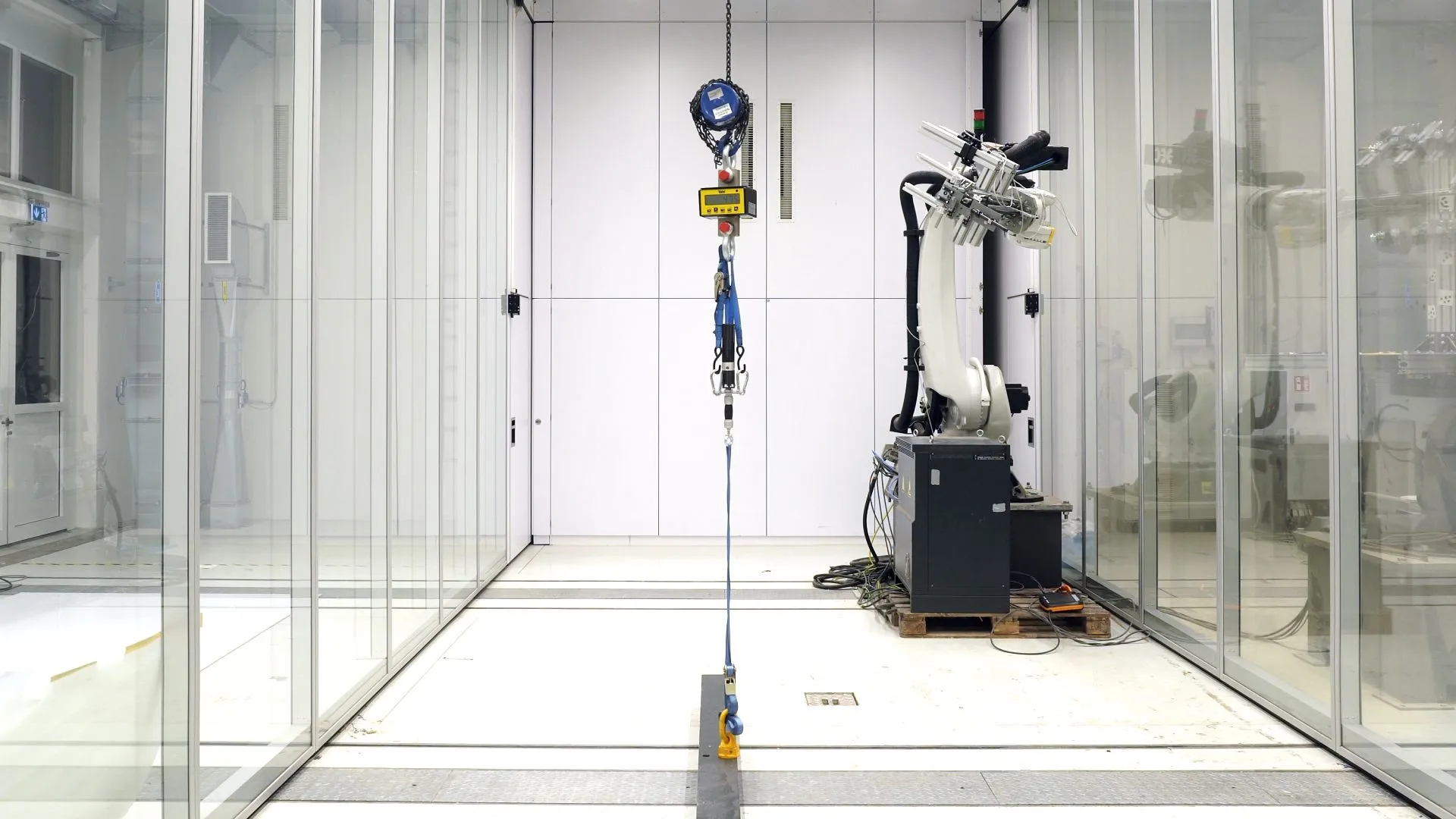
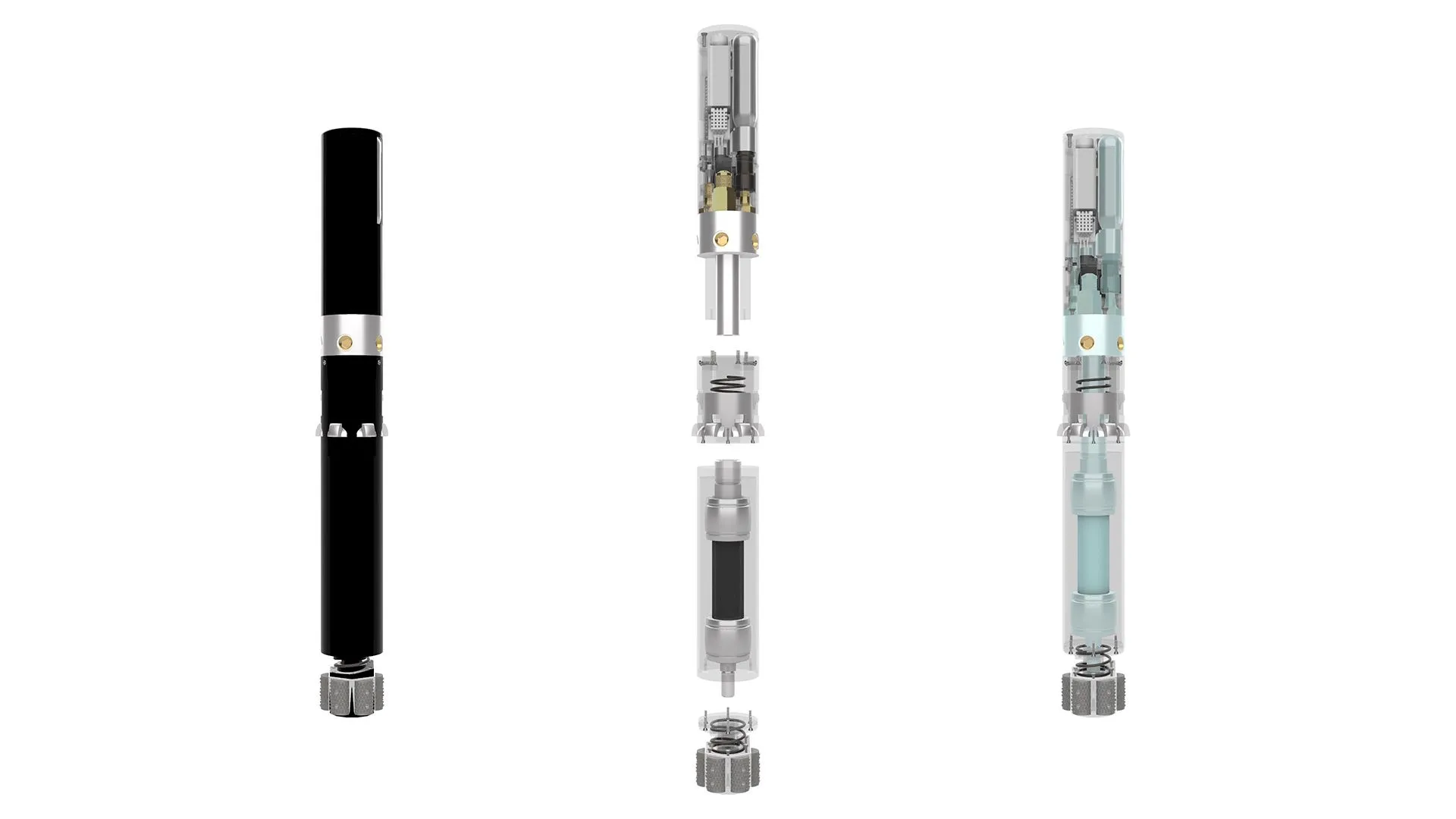
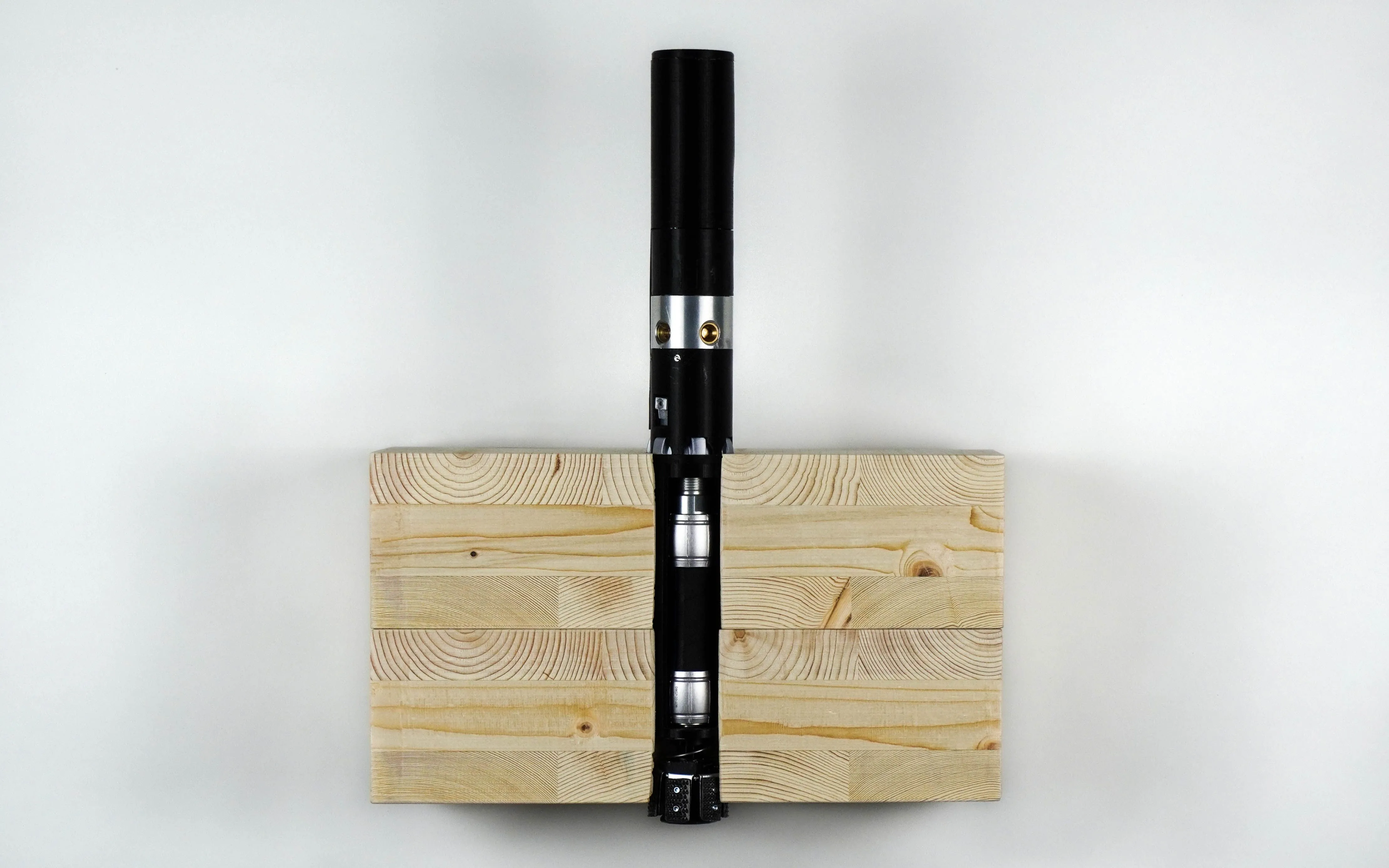
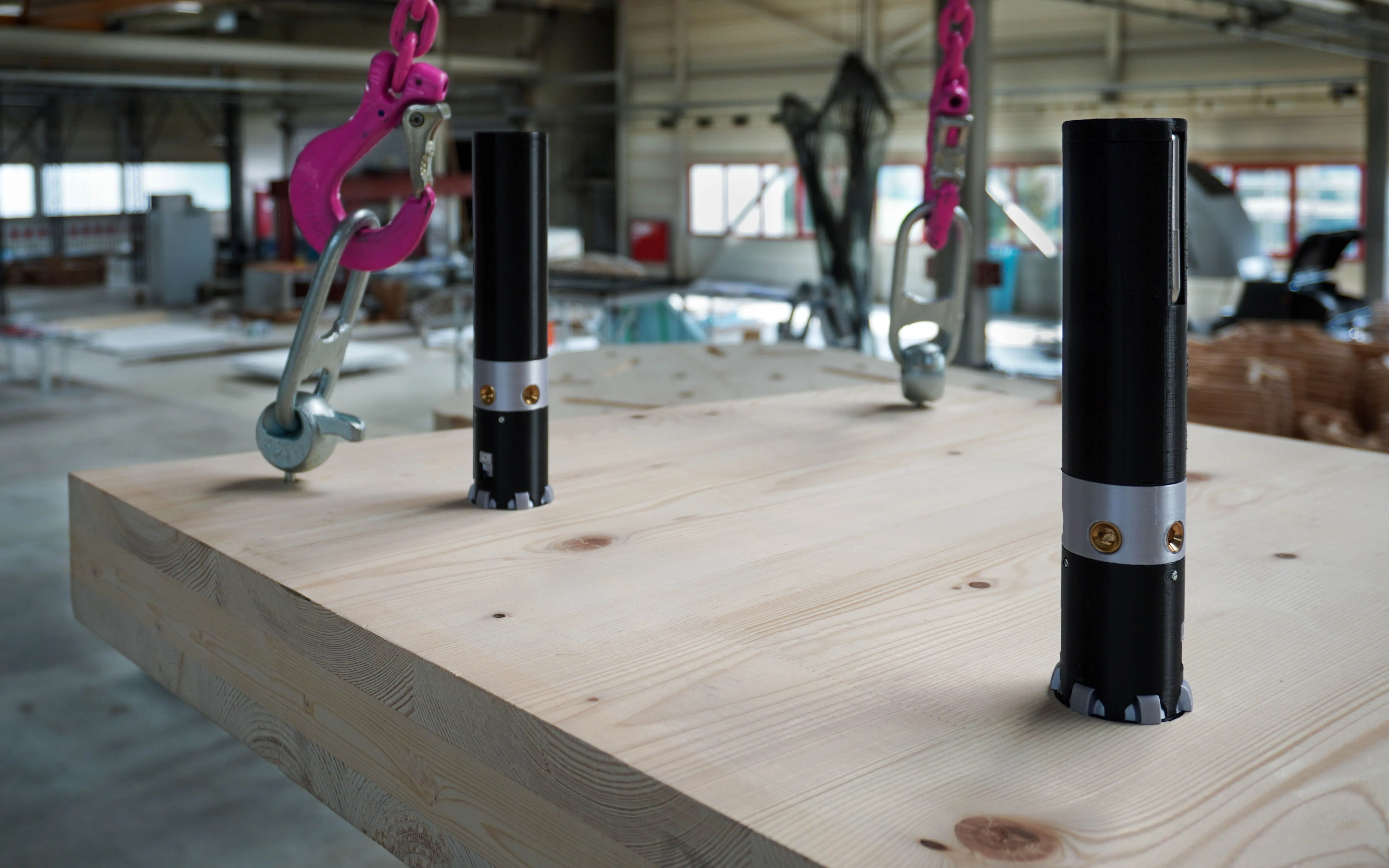
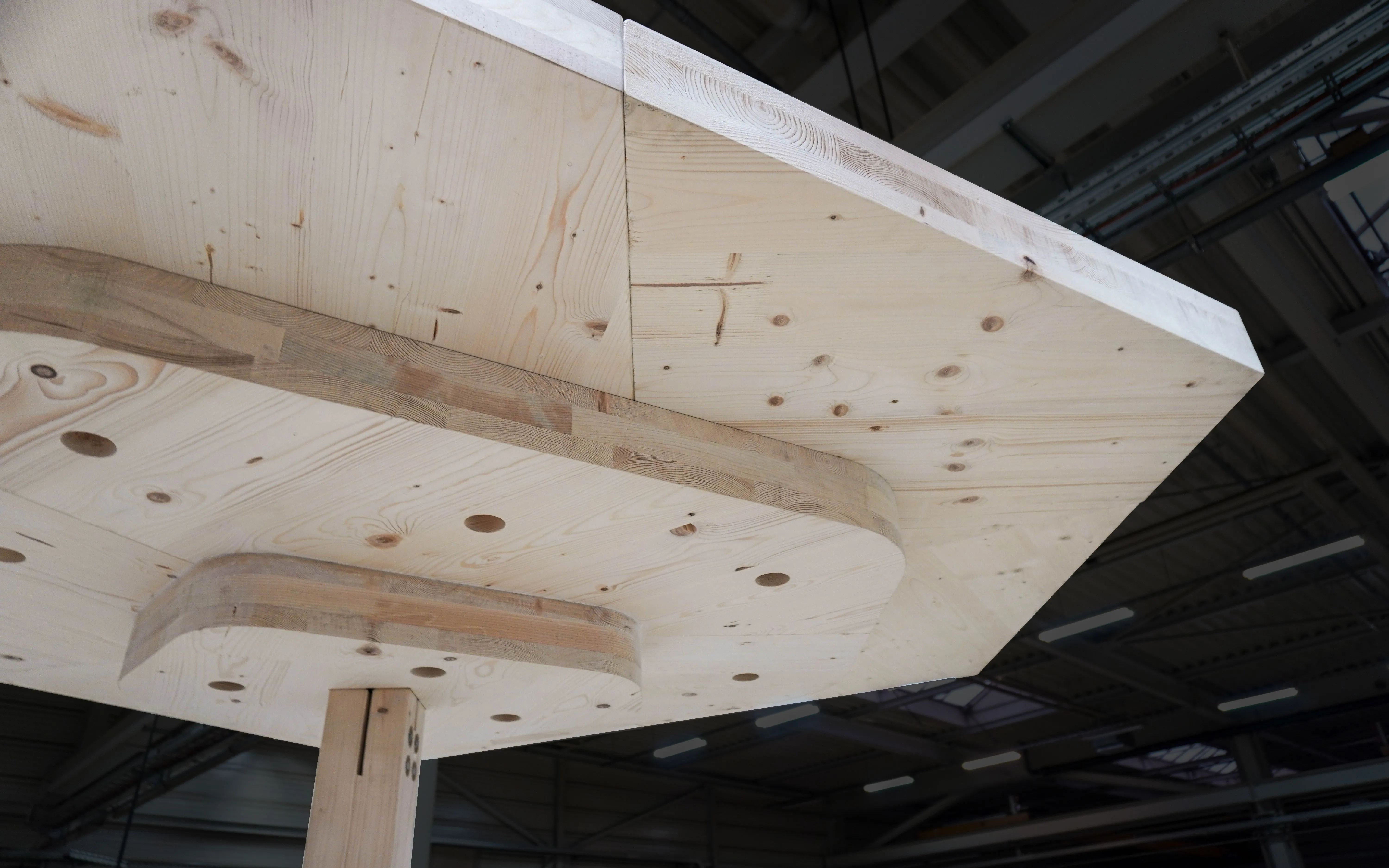
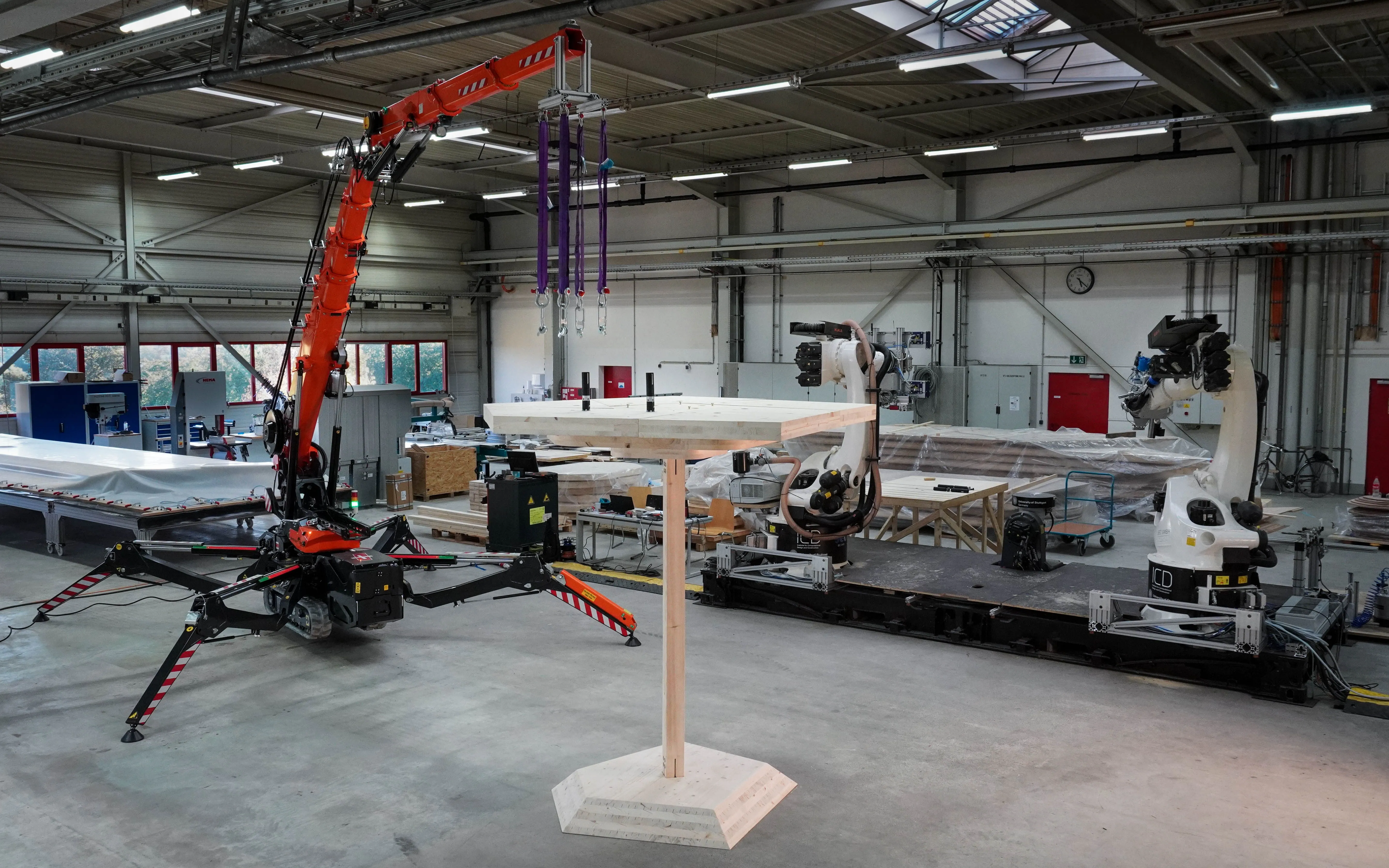
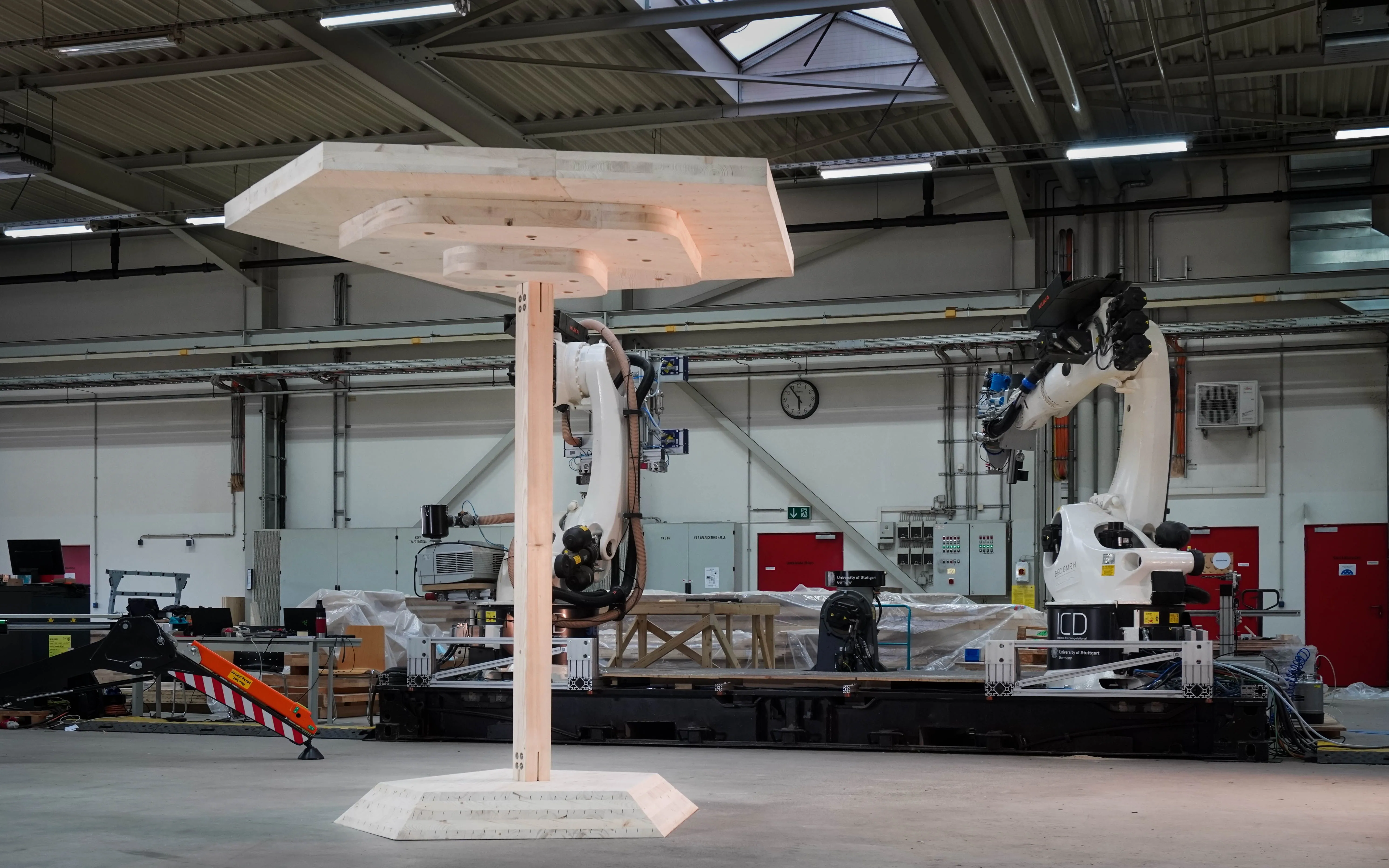
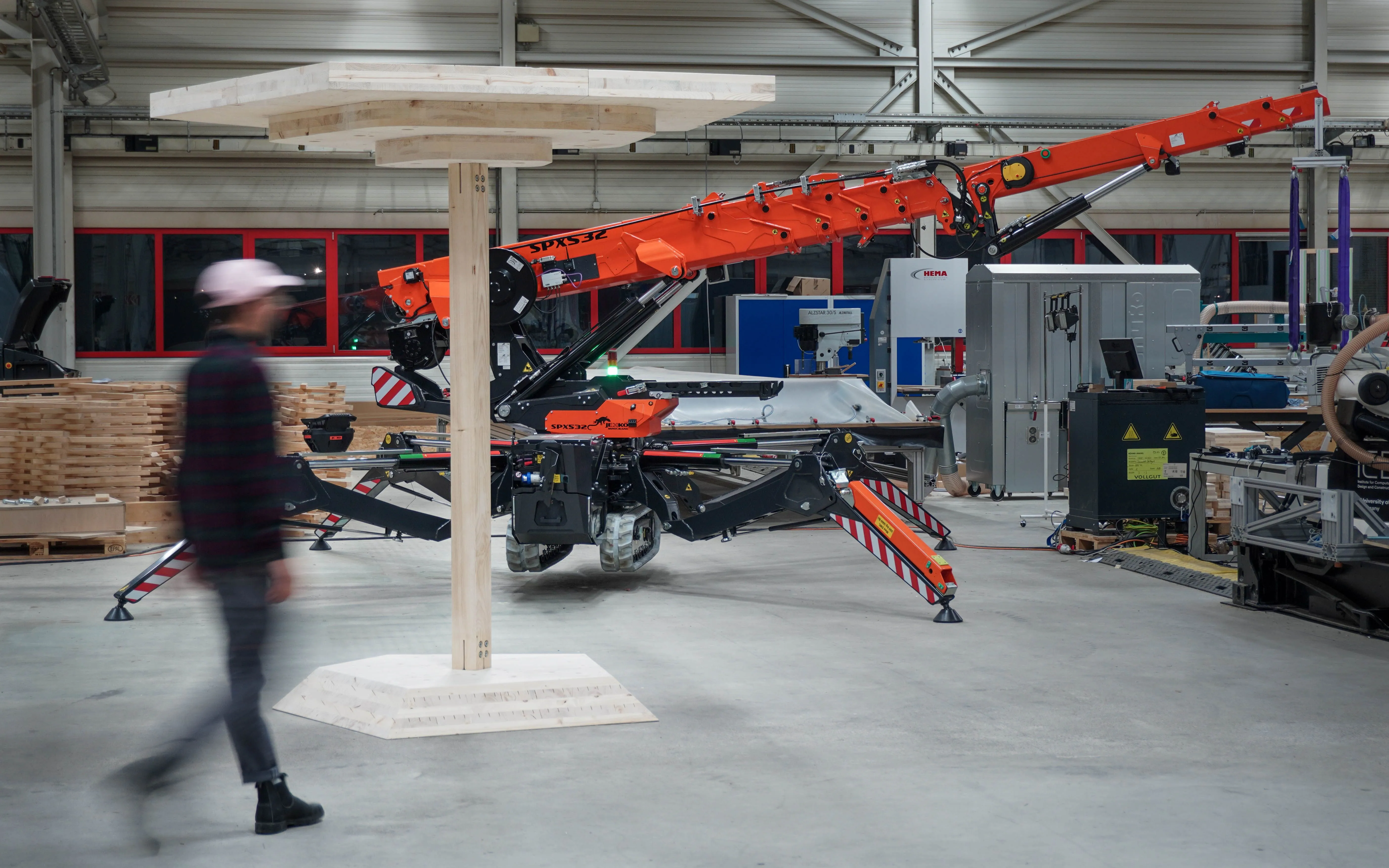
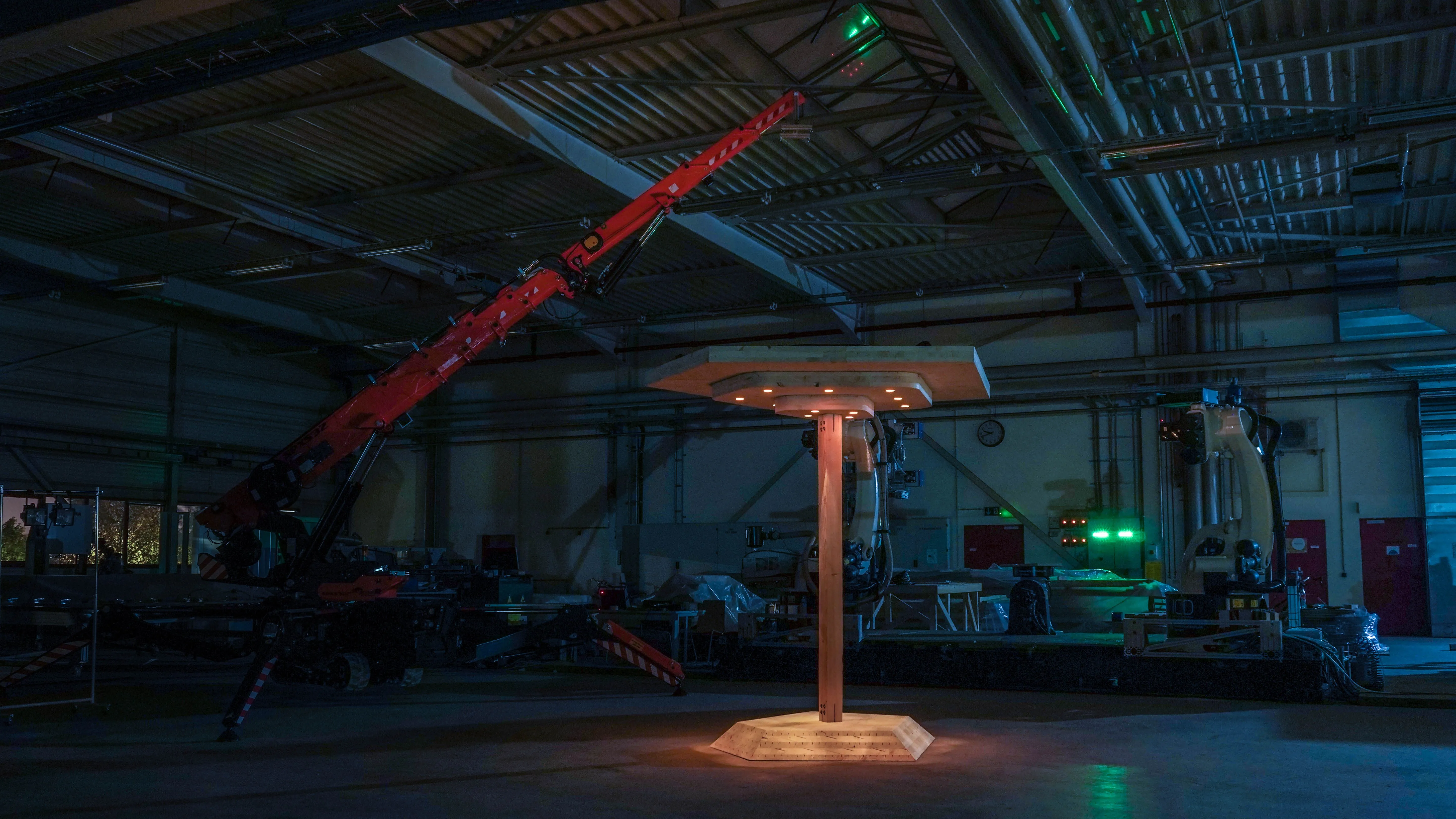